Product Description
Liquid Silicone Rubber Application
Liquid Silicone Rubber injection molding has thousands of applications across a variety of industries, including medical, automotive, infant care, general industrial markets, aerospace, electronics, and many other specialized industries. While liquid silicone rubber injection molding works best for short- and long-run part production, customers can employ the process in the final stages of prototyping. The process is also suitable for the evaluation of different material configurations before green-lighting a project for full production.
Medical: CPAP Mask, Nasal Mask, Medical Grade LSR Gaskets, Bellows, Grommet.
Baby Care: LSR Baby Nipples, Baby Bottles, Baby Bottle Brush, liquid silicone Breast Pump.
Automation: High precision liquid silicone gasket seals, LSR rubber keypad buttons
Bathroom Accessory: Liquid Silicone Toilet Seal Washers, Water-contact Gaskets
Liquid Silicone Rubber Advantages
- Biocompatibility: Under extensive testing, liquid silicone rubber has demonstrated superior compatibility with human tissue and body fluids. In comparison to other elastomers, liquid silicone rubber is resistant to bacteria growth and will not stain or corrode other materials. LSR is also tasteless and odorless and can be formulated to comply with stringent FDA requirements. The material can be sterilized via a variety of methods, including steam autoclaving, ethylene oxide (ETO), gamma, e-beam and numerous other techniques.
- Durable: Liquid Silicone Rubber parts can withstand extreme temperatures, which makes them an ideal choice for components under the hood of cars and in close proximity to engines. Parts fabricated via liquid silicone rubber injection molding are fire retardant and will not melt— a serious problem for components created through plastic injection molding methods.
- Chemical resistance: Liquid Silicone Rubber resists water, oxidation and some chemical solutions such as acids and alkali.
- Temperature resistance: Compared to other elastomers, molded silicone can withstand a wide range of high/low-temperature extremes. For example, Silastic LSR by Dow Corning for continuous use can remain stable through temperatures ranging from –60°C to +180°C.
- Mechanical properties: Liquid Silicone Rubber has good elongation, high tear and tensile strength, excellent flexibility and a hardness range of 5 to 80 Shore A.
- Electrical properties: Liquid Silicone Rubber has excellent insulating properties, which offer an appealing option for a host of electrical applications. Compared to conventional insulating material, silicone can perform in far higher and lower temperatures.
- Transparency and pigmentation: Liquid Silicone Rubber possesses a natural transparency, this attribute makes it possible to produce, colorful, custom, molded products.
Why Chose Liquid Silicone Rubber Molding for Your Products
- High-volume production: Advanced LSR materials offer manufacturers the opportunity for cost-effective, high-volume production of complex liquid silicone injection molding parts.
- Low chance of contamination: The LSR fabrication process takes place in a closed system, which reduces the possibility of contamination because the operator does not have to touch the material, and it is not exposed to the environment.
- Higher level of automation: While the silicone gum rubber process is very labor intensive, LSR allows for the automation of injection equipment, tooling, and ejection equipment. This results in minimal labor cost to monitor the system and change out material drums.
- Quick cycle time: The cycle time for LSR components is shorter than compression molding silicone rubber products.
- High-Precision: Liquid Silicone Products are with very accurate dimensions, minimal flashing. The tolerance can be ±0.05mm.
Liquid Silicone Rubber Application
Liquid Silicone Rubber injection molding has thousands of applications across a variety of industries, including medical, automotive, infant care, general industrial markets, aerospace, electronics, and many other specialized industries. While liquid silicone rubber injection molding works best for short- and long-run part production, customers can employ the process in the final stages of prototyping. The process is also suitable for the evaluation of different material configurations before green-lighting a project for full production.
Medical: CPAP Mask, Nasal Mask, Medical Grade LSR Gaskets, Bellows, Grommet.
Baby Care: LSR Baby Nipples, Baby Bottles, Baby Bottle Brush, liquid silicone Breast Pump.
Automation: High precision liquid silicone gasket seals, LSR rubber keypad buttons
Bathroom Accessory: Liquid Silicone Toilet Seal Washers, Water-contact Gaskets
Liquid Silicone Rubber Advantages
- Biocompatibility: Under extensive testing, liquid silicone rubber has demonstrated superior compatibility with human tissue and body fluids. In comparison to other elastomers, liquid silicone rubber is resistant to bacteria growth and will not stain or corrode other materials. LSR is also tasteless and odorless and can be formulated to comply with stringent FDA requirements. The material can be sterilized via a variety of methods, including steam autoclaving, ethylene oxide (ETO), gamma, e-beam and numerous other techniques.
- Durable: Liquid Silicone Rubber parts can withstand extreme temperatures, which makes them an ideal choice for components under the hood of cars and in close proximity to engines. Parts fabricated via liquid silicone rubber injection molding are fire retardant and will not melt— a serious problem for components created through plastic injection molding methods.
- Chemical resistance: Liquid Silicone Rubber resists water, oxidation and some chemical solutions such as acids and alkali.
- Temperature resistance: Compared to other elastomers, molded silicone can withstand a wide range of high/low-temperature extremes. For example, Silastic LSR by Dow Corning for continuous use can remain stable through temperatures ranging from –60°C to +180°C.
- Mechanical properties: Liquid Silicone Rubber has good elongation, high tear and tensile strength, excellent flexibility and a hardness range of 5 to 80 Shore A.
- Electrical properties: Liquid Silicone Rubber has excellent insulating properties, which offer an appealing option for a host of electrical applications. Compared to conventional insulating material, silicone can perform in far higher and lower temperatures.
- Transparency and pigmentation: Liquid Silicone Rubber possesses a natural transparency, this attribute makes it possible to produce, colorful, custom, molded products.
-
Why Chose Liquid Silicone Rubber Molding for Your Products
- High-volume production: Advanced LSR materials offer manufacturers the opportunity for cost-effective, high-volume production of complex liquid silicone injection molding parts.
- Low chance of contamination: The LSR fabrication process takes place in a closed system, which reduces the possibility of contamination because the operator does not have to touch the material, and it is not exposed to the environment.
- Higher level of automation: While the silicone gum rubber process is very labor intensive, LSR allows for the automation of injection equipment, tooling, and ejection equipment. This results in minimal labor cost to monitor the system and change out material drums.
- Quick cycle time: The cycle time for LSR components is shorter than compression molding silicone rubber products.
- High-Precision: Liquid Silicone Products are with very accurate dimensions, minimal flashing. The tolerance can be ±0.05mm.Liquid Silicone Rubber Application
Liquid Silicone Rubber injection molding has thousands of applications across a variety of industries, including medical, automotive, infant care, general industrial markets, aerospace, electronics, and many other specialized industries. While liquid silicone rubber injection molding works best for short- and long-run part production, customers can employ the process in the final stages of prototyping. The process is also suitable for the evaluation of different material configurations before green-lighting a project for full production.
Medical: CPAP Mask, Nasal Mask, Medical Grade LSR Gaskets, Bellows, Grommet.
Baby Care: LSR Baby Nipples, Baby Bottles, Baby Bottle Brush, liquid silicone Breast Pump.
Automation: High precision liquid silicone gasket seals, LSR rubber keypad buttons
Bathroom Accessory: Liquid Silicone Toilet Seal Washers, Water-contact Gaskets
Liquid Silicone Rubber Advantages
- Biocompatibility: Under extensive testing, liquid silicone rubber has demonstrated superior compatibility with human tissue and body fluids. In comparison to other elastomers, liquid silicone rubber is resistant to bacteria growth and will not stain or corrode other materials. LSR is also tasteless and odorless and can be formulated to comply with stringent FDA requirements. The material can be sterilized via a variety of methods, including steam autoclaving, ethylene oxide (ETO), gamma, e-beam and numerous other techniques.
- Durable: Liquid Silicone Rubber parts can withstand extreme temperatures, which makes them an ideal choice for components under the hood of cars and in close proximity to engines. Parts fabricated via liquid silicone rubber injection molding are fire retardant and will not melt— a serious problem for components created through plastic injection molding methods.
- Chemical resistance: Liquid Silicone Rubber resists water, oxidation and some chemical solutions such as acids and alkali.
- Temperature resistance: Compared to other elastomers, molded silicone can withstand a wide range of high/low-temperature extremes. For example, Silastic LSR by Dow Corning for continuous use can remain stable through temperatures ranging from –60°C to +180°C.
- Mechanical properties: Liquid Silicone Rubber has good elongation, high tear and tensile strength, excellent flexibility and a hardness range of 5 to 80 Shore A.
- Electrical properties: Liquid Silicone Rubber has excellent insulating properties, which offer an appealing option for a host of electrical applications. Compared to conventional insulating material, silicone can perform in far higher and lower temperatures.
- Transparency and pigmentation: Liquid Silicone Rubber possesses a natural transparency, this attribute makes it possible to produce, colorful, custom, molded products.
Why Chose Liquid Silicone Rubber Molding for Your Products
- High-volume production: Advanced LSR materials offer manufacturers the opportunity for cost-effective, high-volume production of complex liquid silicone injection molding parts.
- Low chance of contamination: The LSR fabrication process takes place in a closed system, which reduces the possibility of contamination because the operator does not have to touch the material, and it is not exposed to the environment.
- Higher level of automation: While the silicone gum rubber process is very labor intensive, LSR allows for the automation of injection equipment, tooling, and ejection equipment. This results in minimal labor cost to monitor the system and change out material drums.
- Quick cycle time: The cycle time for LSR components is shorter than compression molding silicone rubber products.
- High-Precision: Liquid Silicone Products are with very accurate dimensions, minimal flashing. The tolerance can be ±0.05mm.
Payment Terms︰
TT/Paypal
Product Image
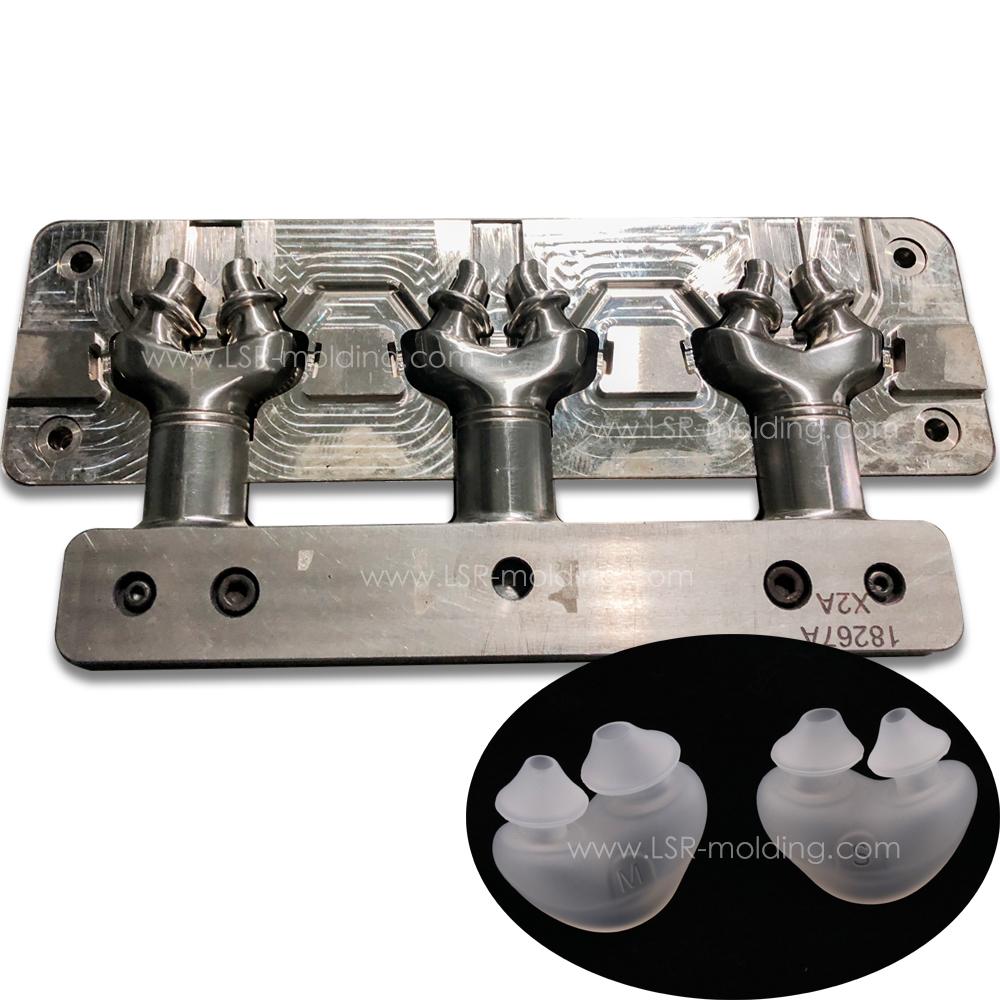

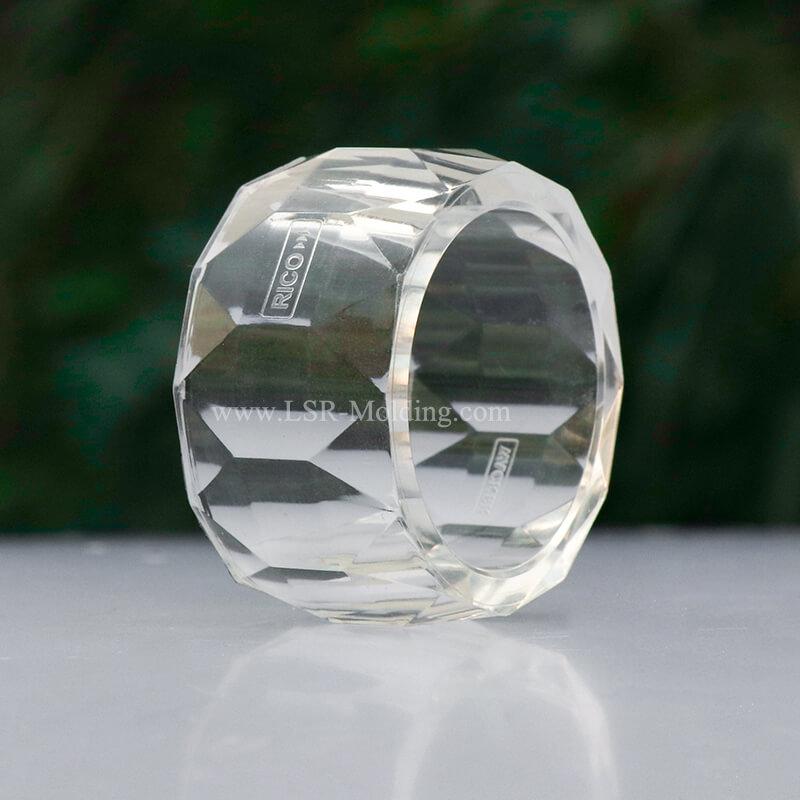
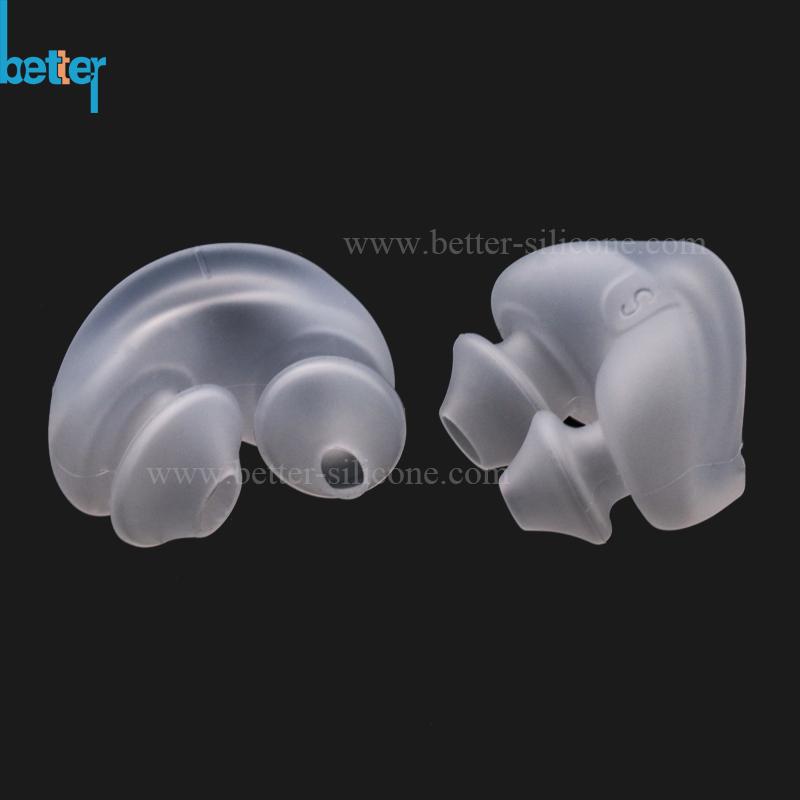
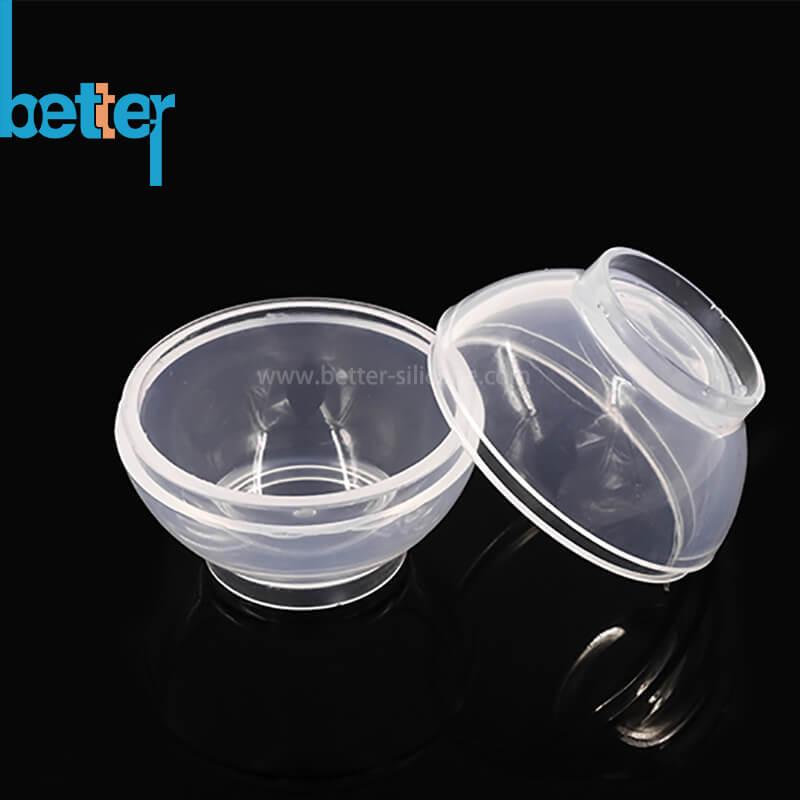